Recent Articles
Nic Johnsen leads Fire Protection Engineering
Johnsen’s holistic approach adds value through performance-based design, informed by contracting and risk-management experience.
Steven Andersen promoted to National Laboratory Specialist
The new position establishes a national resource for all LEO A DALY studios and markets to offer best-in-class laboratory design
Ed Benes, PE, named President and Deputy CEO
Benes will work closely with Leo A. Daly III, the firm’s third-generation owner and CEO, to shape the future of LEO A DALY
Minnesota Army National Guard Division Headquarters wins SAME Grand Design Award
Recognized as one of the best works of federal architecture built this decade, the LEO A DALY-designed facility reimagines the National Guard readiness center for a new era of warfighting, peacekeeping and emergency response missions
LEO A DALY transforms Capitol Hill office building into mixed-use development
The $200 million project will add three stories, a new skin and a vibrant mix of uses to a former government building
Five years later, Cobalt is a model of sustainable design
The Omaha World Herald interviewed LEO A DALY’s Martin Janousek, AIA, about Cobalt Credit Union’s award-winning sustainable headquarters
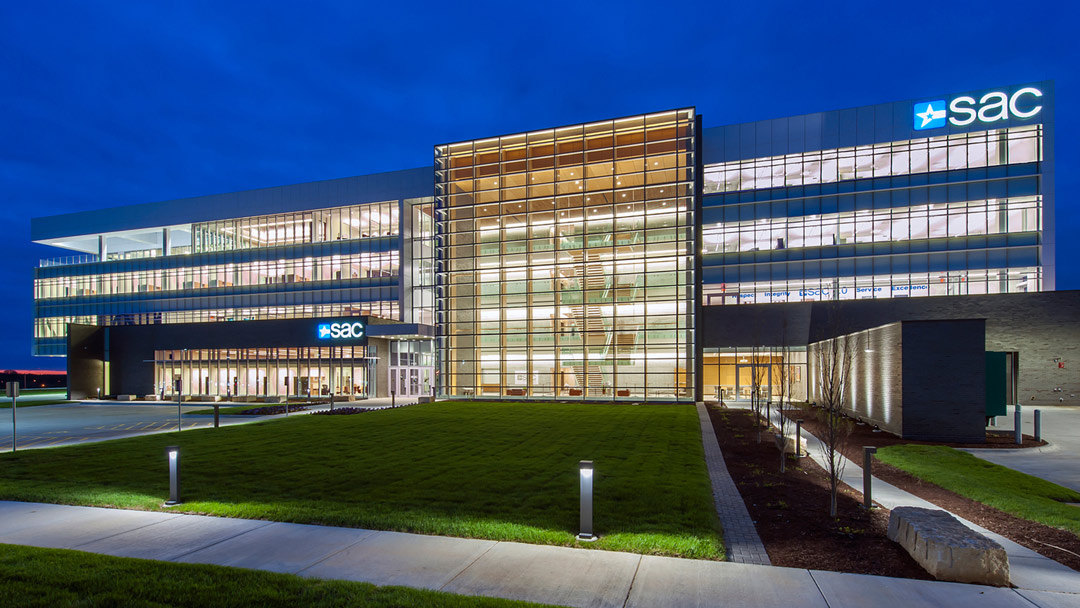
Excerpted from the article by Jeff Barnes:
With functions scattered throughout the Bellevue area, Cobalt Credit Union had the opportunity to do things differently in constructing a new headquarters building five years ago.
Visibility for the credit union was important, said Martin Janousek, senior design architect with Leo A Daly. “But what they wanted in environmental responsibility and sustainability was just as necessary.”
Hidden beneath the southern landscape of the headquarters on the southeast corner of 72nd Street and Nebraska Highway 370 in Papillion are more than 200 geothermal wells connected to heat pumps, moving heat to water when cooling and absorbing heat from water when heating.
While all of that is going on underground, sunlight streams into the four-story atrium while natural light pours into the building from all sides, with automated systems constantly and almost imperceptibly adjusting for the proper light throughout the day.
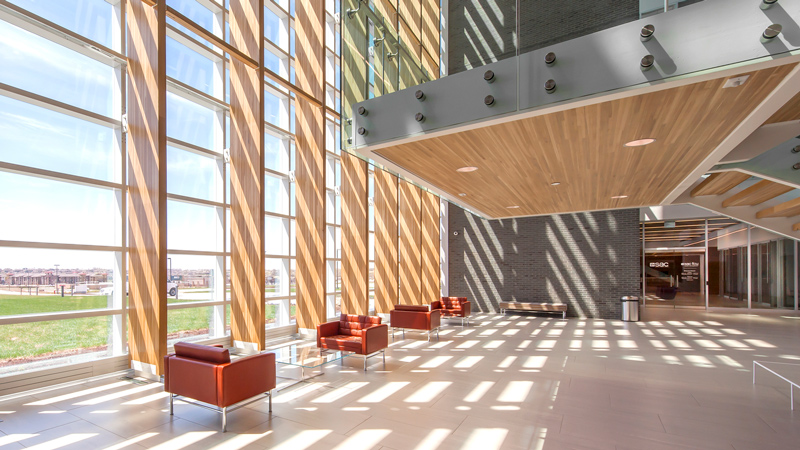
Being the owner as well as occupant allowed the credit union to carry off what building owners typically don’t invest in, Janousek said. “But the client (then known as SAC Federal Credit Union in 2014) knew they were going to stay here when they built and could afford to invest in the technology that would ultimately result in savings for their members.”
Besides providing a field for the geothermal wells, the Sarpy County setting provides for the heavy use of natural grass. It enhances the dramatic views from the building’s south, supplemented by water-retention ponds for rain runoff. The result is a natural, yet low-maintenance footprint for the site.
For the Cobalt building, there was a good deal of metaphorical design. The first floor, for example, makes heavy use of dark brick reflecting the solidity of the credit union’s membership base.
“The first floor is a very public space, with a branch bank, community rooms and other accessible spaces,” Janousek said. “It holds up the building, just as the membership solidly supports the credit union.”
As you rise to higher floors, Janousek said, the space gets more open and lighter, through heavy use of steel and glass to bring in four stories of natural light to emphasize openness and transparency in the institution’s management and operation.
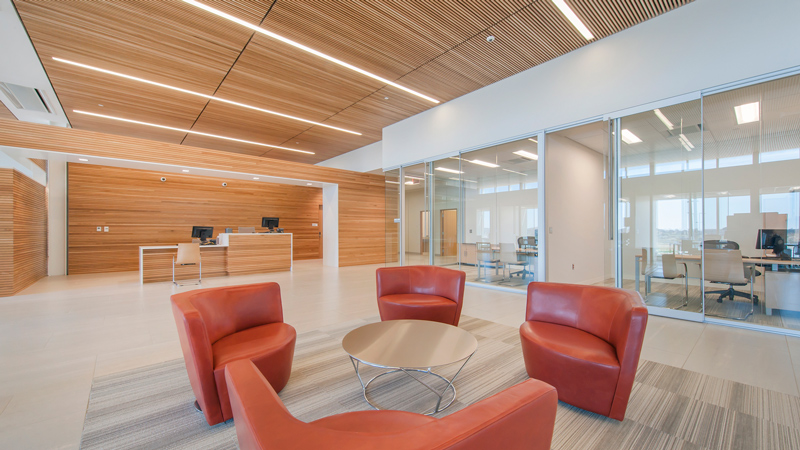
It also contributes to the corporate culture of the building. Because many employees were at sites outside of the previous headquarters building, it was important to bring them all together and working as a team. The communications-core atrium gives a common area to all floors and its “floating staircase” encourages a common traveling area and sense of community throughout the floors as employees talk and meet on the stairs. The airiness continues to a fourth-floor balcony and rooftop patio.
The glass atrium contributes to the sense of community and to the wellness of the workforce, Janousek said. “Just the simple thing of natural light in this building contributes,” he said. “Research shows that the more access you have to natural light, the happier and healthier you are at your workplace.”
Contributing to the environment, of course, are the materials used in the building and how they are made and assembled. Janousek said locally produced materials were employed whenever possible, such as brick from Endicott Brick in Nebraska. Poured concrete was used throughout for its simplicity, durability and low maintenance.
“We used a unitized curtain wall system for its construction,” Janousek said, “which was all assembled in an offsite warehouse, shipped by truck and hoisted into place. We weren’t relying on good weather to install the curtain wall, a tremendous savings to construction costs.”

Recycled carpeting and other second-life materials are incorporated throughout. Leo A Daly found a manufacturer with a large supply of white oak and no use for the wood — that became part of the four-story columns in the atrium.
Beneath the skin of the walls, floors and ceilings bring all manner of energy savings and innovation. The building makes extensive use of the chilled-beam system, in which chilled water passes through tubes in the ceiling, warm air from the space rises toward the ceiling, and the air surrounding the chilled beam is cooled and falls back toward the floor, creating convective air motion to cool the space without the use of a fan.
“They were one of the first in the area to use the chilled-beam system as opposed to a forced-air system,” Janousek said. “Without all of the duct work, it eliminates a lot of the space formerly necessary between floors and eliminates all of the noise of forced-air.”
The building uses radiant heat for warming and a heat capture system to save and reuse heat that would otherwise be lost. Motion-activated LED lighting automatically adjusts based on the light coming into the building. The result? An estimated 30% savings on utility costs.
“(Cobalt) wanted to be good stewards of the environment, and we showed them what they could do and what the paybacks would be in the long run,” Janousek said. “Making these efforts shows significant savings as compared to a code-compliant building of today.”
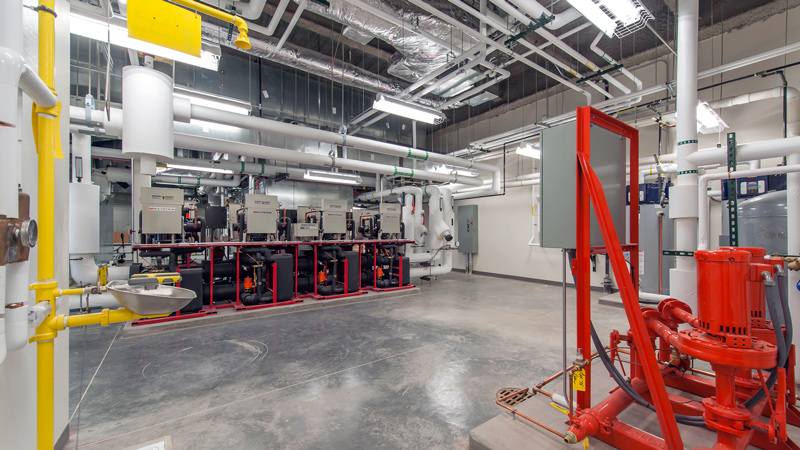